Normal Strain
Change in the length divided by the original length is called normal strain.
Shear Strain
Change in angle or shape of to the original angle or shape of the body is called shear strain.
Mechanical Strain gauges
They can measure the surface strains in any direction. We place gauge parallel to the surface in which direction we want to measure the strains. It can measure static strains only.
Optical Strain gauges:
In these gauges the measurement and magnification are done optically. A system of mirrors may be used to produce large displacement on scale. It is suitable for measuring dynamics strains with a photographic recording system. It is difficult to handle and is a heavy instrument.
Vibrating wire type gauges
When wire is stretched between two clamps the natural frequency will change. This principle is used to measure the strains in vibrating wire type gauges. A gauge containing the wire is clamped into the test piece and frequency of vibrations is measured. Then it is compared to with the standard known frequency.
Easy and rapid measurement of strains can be done by this type of gauge.
Pneumatic Strain gauges
This type of strain gauge is very widely used in precise engineering measurement to measure the micro strains. These gauges have very little application in Civil engineering. Working principle of Pneumatic gauges is that pressure drop is directly proportional to amount of fluid passing through the orifice.
It has stability over larger period and high degree of precision.
Electrical Resistance Strain gauge
It is a very fine metal grid which is cemented in paper base material on the surface of the any structural component to measure the surface normal strains in any desired direction.
Lord Kevin (1856) first gives the principle of working of strain gauges. He proved that the resistance of conductor changes with the change in length. The idea was used to measure the strain first in 1936 by US Defense department.
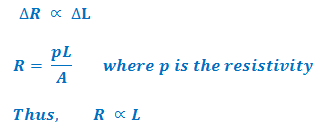
Construction of strain gauge
- Length of filament varies from 2 to 25mm. Normally 10- 25mm is used for tension members and 2-4mm for compression members.
- Safe current is 25mA – 50 mA.
- Range of voltage is 35 – 50 V
- Metal used are Copper (55%) + Nickel (45%) Alloy or can be Nickel + Chromium Alloy
Axial Sensitivity of strain gauges
The change in the resistance of a wire is directly proportional to axial sensitivity of the strain gauge. It is also called gauge factor (G.F).
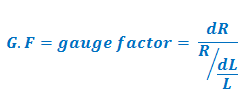
Dummy gauge
A strain gauge of the same resistance and sensitivity as that of the actual gauge and is cemented on a separate piece of material of the same type and is kept in the unrestrained condition in the vicinity of that actual gauge called dummy gauge. The work of dummy gauge is to nullify the effect of the temperature changes. If, A is the Strain due to change in length and B is strain due to temperature change then,
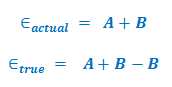
Advantages of Electric Resistnace Gauge
- Normal strains can be measured in any desired direction on surface of the structural component.
- Shear strains can be measured by using some special arrangements.
- Remote reading is possible.
- Once the strain gauge is cemented it will be long period of time until the bond between strain gauge and component breaks.
- Static as well as dynamic strains can be measured.
- Strain can be measured in any desired position e.g Top fibers, bottom fibers and at neutral axis.